Interior metal skin vapour barrier
FIREsafe/ FIBERfree
high performance insulation
high performance insulation
Superior airtightness Guaranteed
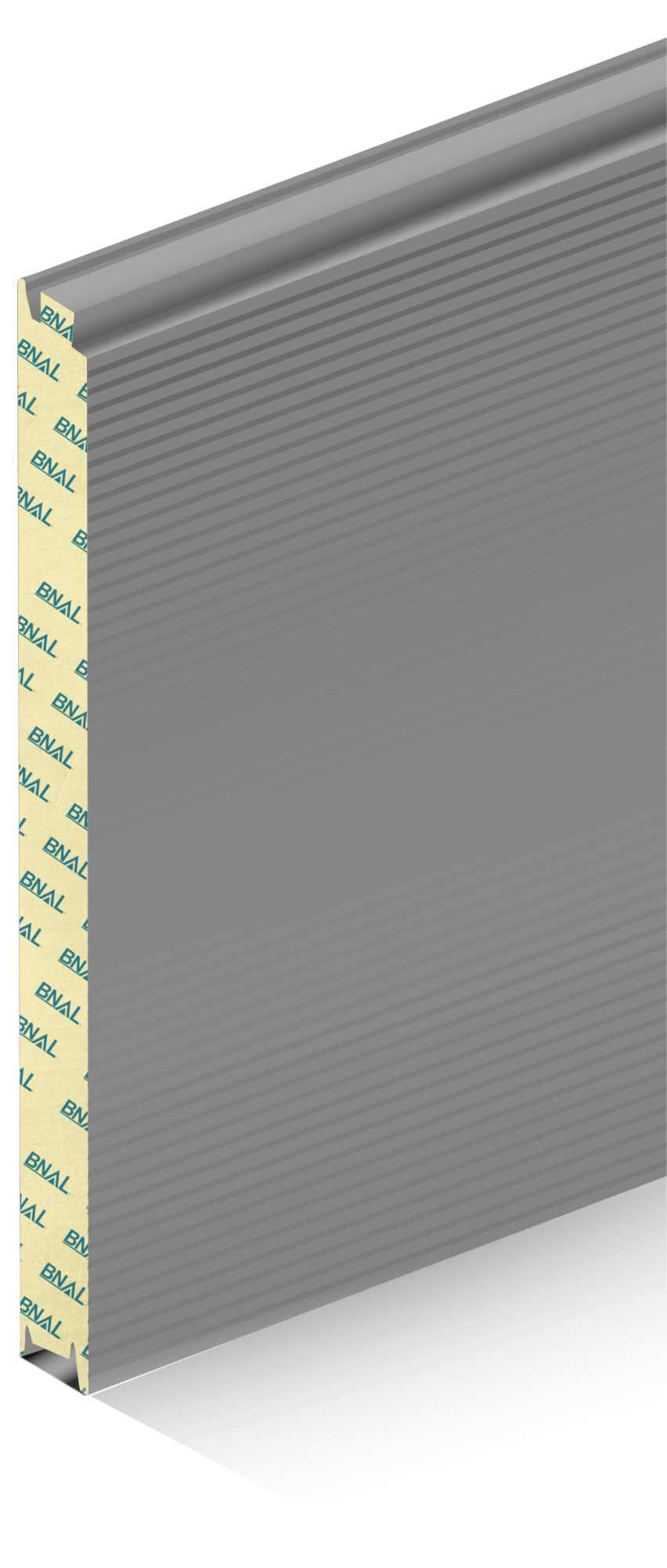
Single-component, single-fix system promotes accelerated build speed
Exterior metal skin weather barrier
Constructed the Auditorium for the Rezangala War memorial using LGSF Technology at an height of more than 15500 foot above sea level. This was executed by BNAL within a record time of 1 month and was greatly appreciated by all concerned. The memorial has been made to commemorate the supreme sacrifice made by 114 Brave Hearts of the Indian Army and was dedicated to the nation by the Hon’ble Defence Minister of India Shri Rajnath Singh on 18th November 2021.
Recently completed Aircraft Hangar with motorised gates and double storey annexes on both sides.
The hangar was completed from start to finish within 5 months making it possibly the fastest
construction for an Aircraft Hangar in India.
Double Storey Three Bedroom Prefabricated Cottage
using the latest state of the art LGSF technology.
Executed PEB works for 7 nos. of Indoor Sports stadiums at various Government Schools in Chandigarh.
The Buildings have a clear span of 62 Meters and total area executed is 2,70,000 sq. ft.
BNAL has executed complete turnkey project for NTPC at Hazaribagh. The scope of work included design, Manufacture, Supply and Erection of Single and Multi-Storey Prefabricated Structures including all Civil, Electrical, Sanitary and Plumbing Works. Total Area Executed – 65000 sq. ft. appx.
Quality:
We are committed to delivering products and services of the highest quality that meet or exceed customer expectations.
Innovation:
We are constantly seeking new and innovative ways to improve our products, processes, and services to better serve our customers and stay ahead of the competition.
Ethics:
We operate with integrity, honesty, and transparency in all our dealings with customers, suppliers, employees, and other stakeholders.
Cost-effectiveness:
We are committed to providing cost-effective solutions without compromising on quality or timelines.
Customer Focus:
We are dedicated to understanding and meeting the needs of our customers and building long-term relationships based on trust, reliability, and value.
Customer Focus:
We are dedicated to understanding and meeting the needs of our customers and building long-term relationships based on trust, reliability, and value.
Sustainability:
We are committed to reducing our environmental impact and promoting sustainable practices throughout our operations and supply chain.
Safety:
We prioritize the safety and well-being of our employees, customers, and communities in all aspects of our business.
Industry Leading Technology:
We are committed to employing technology in construction that ensures zero impact on the ozone layer and does not contribute to its depletion
Commitment:
We focus on solution delivery with complete adherence to service quality standards and zero deviation from committed timelines